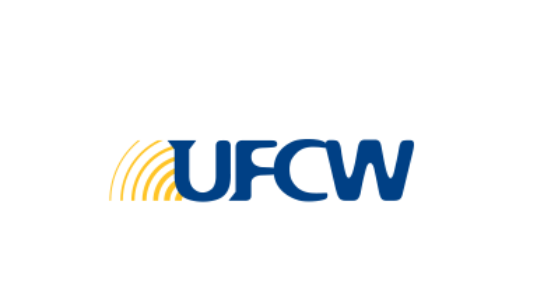
RWDSU Post Cereal Workers in Michigan Ratify a New Contract
January 31, 2024
Viewing 1-10 results of 277
RWDSU Post Cereal Workers in Michigan Ratify a New Contract
January 31, 2024
Ben & Jerry’s Ice Cream Workers Join Local 371
January 4, 2024
RWDSU Quaker Oats Workers in Iowa Ratify a New Contract
December 1, 2023
Conagra Maintenance Workers in Indiana Join Local 700
December 1, 2023
PSSI Workers in Kansas Join Local 2
November 17, 2023
Hormel Foods Workers Ratify Historic Contract
October 18, 2023
Home Chef Workers in Illinois Join Local 1546
October 12, 2023
Poultry Workers in California Join Local 8GS
August 23, 2023
PSSI Workers in Texas Join Local 540
August 4, 2023
Poultry Workers in New Jersey Ratify a New Contract
May 17, 2023